Helical Gearboxes Are As a Mainstay of Steel Plant Effectiveness
Plastic extrusion, a groundwork of up-to-the-minute manufacturing, demands full-bodied and consistent machinery capable of consistently delivering high-quality products under demanding operating conditions. Essential to this process is the extrusion screw, driven by a controlling motor and meticulously controlled by a crucial component: the worm reduction gearbox.
These specific quality gearboxes by Gamma Gears is worm gear reducer gearbox manufacturer in Ahmedabad, Gujarat, India, are not merely components; they are the backbone of effective and productive plastic extrusion plants, ensuring prime performance and durability.
Considerate the Role of Worm Reduction Gearboxes in Extrusion
Plastic extrusion involves melting and shaping thermoplastic materials through a heated die. The extrusion screw, a rotating helical shaft within a barrel, is responsible for conveying, melting, and pressurizing the polymer. This process necessitates significant torque and precise speed control. This is where the worm reduction gearbox steps in.
Gamma Gears is world’s one of the best gearbox manufacturing company in Ahmedabad, Gujarat, India and the primary function of a worm reduction gearbox in a plastic extrusion plant is to reduce the high speed of the motor to a lower, more powerful rotational speed at the output shaft connected to the extrusion screw. This speed reduction is crucial for several reasons:
Increased Torque: Worm reduction gearboxes best at providing high torque multiplication. This is mainly main for processing high-viscosity materials or extruding large profiles.
Precise Speed Control: Precise control over the extrusion process is supreme and vital for maintaining consistent product quality and dimensional accuracy. Worm gearboxes allow for fine-tuning of the extrusion screw speed, ensuring optimal material flow and product consistency.
Smooth Mechanical Operation: The inherent geometry of worm gears leads to characteristically smooth, quiet operation. This reduces wear and tear on the gearbox itself and on other components of the extrusion line, contributing to reduced maintenance requirements.
Self-Locking Capabilities: Many worm gearboxes possess a self-locking – self disconnected or disconnected characteristic. This means that when the motor is disengaged, the gearbox prevents the extrusion screw from rotating backward under the force of the molten polymer. This is a vital security feature.
High Quality Key Concerns for Worm Reduction Gearboxes
Choosing the right worm reduction gearbox is important for optimizing the extrusion process. Several factors must be carefully considered:
Torque Requirements: The gearbox must be rated for the required torque output to successfully extrude the chosen material and profile size. Underestimating this requirement can lead to early failure.
Gearbox Speed Ratio: The desired speed reduction ratio dictates the gearbox’s gear configuration. Precise calculation of the optimal ratio ensures efficient operation and optimal performance of the extrusion screw.
Machinery Material Compatibility: The worm gear reducer gearbox materials need to be compatible with the operating temperature and the potentially corrosive nature of certain polymers. This frequently necessitates the use of specialized materials.
Mechanical Output Effectiveness: Gearbox efficiency directly influences energy consumption. Selecting a high-efficiency gearbox minimizes operating costs and contributes to a more environmentally friendly production process.
Mounting and Integration: The gearbox’s mounting dimensions and design should seamlessly integrate into the overall extrusion line layout, minimizing installation complexities and ensuring proper alignment.
Maintenance Requirements: Choosing a gearbox with negligible maintenance requirements contributes to reduced downtime and operational efficiency. Systematic lubrication and inspection are crucial for maintaining optimal performance.
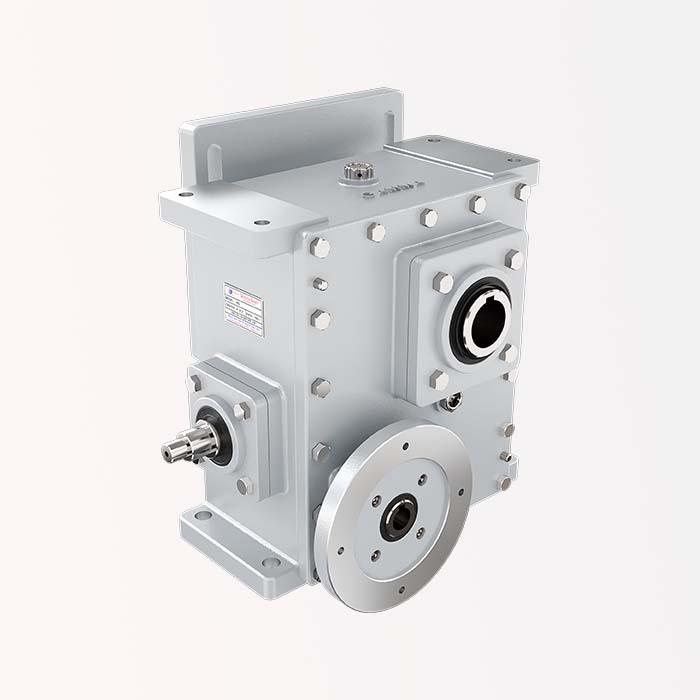
Engineering Advancements in Worm Reduction Gearbox
Continuous advancements in materials science and manufacturing techniques have led to significant improvements in worm reduction gearbox technology for plastic extrusion applications. These include better-quality materials, heightened gear profiles, enhanced lubrication systems and integrated monitoring systems.
Worm reduction gearboxes provide high torque, precise speed control, and smooth operation ensures efficient and reliable extrusion machinery processes, contact to Gamma Gears is worm gear reducer gearbox manufacturer in Ahmedabad, Gujarat, India.