Helical Gearboxes Are As a Mainstay of Steel Plant Effectiveness
Steel plants are engineering base of industrial power, demanding strong and reliable machinery to operate at peak productivity. At the heart of many key processes lie helical gearboxes, pillars that translate high torque and power into precise, controlled motion. On or after the massive rolling mills to the intricate processes of material handling, these specific helical gearboxes are vital for the smooth, uninterrupted operation of a modern steel plant. Their role is key to comprehending the efficiency and productivity of this vital industry.
Helical gearboxes be at variance from their spur gear counterparts in their tooth design. Rather than straight teeth, helical gears possess teeth that are cut at an angle to the axis of rotation. This superficially minor detail offers significant advantages, mainly in high-power applications like those found in steel plants. The angled teeth allow for a more gradual engagement of teeth, resulting in meaningfully smoother operation and reduced noise compared to spur gears. This smoother operation translates directly into increased efficiency and reduced wear and tear on the complete steel plant machinery system.
From Gamma Gears which is a world’s one of the best worm reduction gearbox manufacturing company in Ahmedabad, Gujarat, India, the most significant benefits of helical gearboxes in steel plants is their ability to handle high torque loads. The rolling mills, for instance, require immense power to shape and form steel at high temperatures. Helical gears’ angled tooth design distributes the load more effectively across multiple teeth simultaneously, resulting in higher load-carrying capacity and reduced stress on individual teeth. The increased contact gear ratio, a measure of how many teeth are in mesh at any given time, further enhances the load-bearing capabilities.
At Gamma Gears, helical gearboxes are high output torque wide range of gear ratio horizontal foot mounting. The gradual engagement of teeth minimizes impact forces, reducing energy loss through friction and vibration. This improved efficiency straight contributes to lower energy consumption, resulting in substantial cost savings for the steel plant over the long term. In an industry where energy costs are a significant factor, this benefit cannot be excessive.
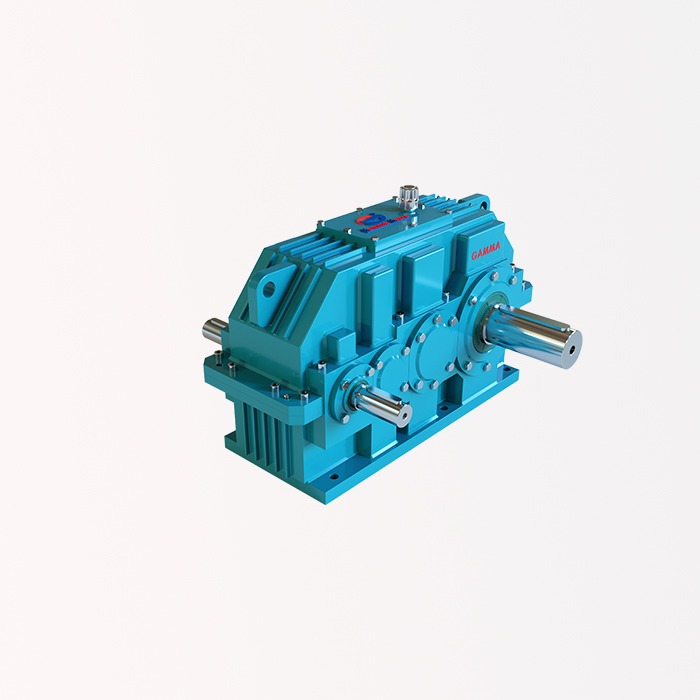
Helical gearboxes provide a higher level of precision and control. In steel plants, even small variations in speed or torque can affect the quality of the final product. The smooth, consistent operation of helical gearboxes ensures particular control over the machinery, contributing to improved product quality and reduced waste. This is principally important in processes like cold rolling, where detailed control over the rolling speed is crucial for achieving the desired thickness and surface finish.
By means of worm reduction gearbox manufacturer Gamma Gears, despite technical considerations, the long-term benefits of increased efficiency, reduced maintenance, and improved product quality generally outweigh the higher initial venture. The robust nature of helical gearboxes ensures extended lifespans, minimizing downtime and replacement costs. The reduced noise pollution is also a significant benefit, improving the working environment for the plant’s employees.
High output torque wide range of gear ratio horizontal foot mounting helical gearbox operate smoothly, and deliver exact control, are a crucial component in maximizing efficiency and productivity. The long-term benefits of reduced energy consumption, minimized downtime, and improved product quality solidify their position as the backbone of many steel plant operations, ensuring the continued flow of steel that fuels modern infrastructure and industry. The asset in robust and efficient helical gearboxes is a secured deal in the future of steel production.