Why Worm Reduction Gearboxes are Essential and Leading for Chemical Plant Industries
Chemical plants are complex ecosystems of machinery, processes, and precision. Inside this difficult network, one component often works determinedly behind the scenes, ensuring the smooth and efficient operation of critical systems: the worm reduction gearbox. While perhaps not as visually imposing as a towering distillation column or a gleaming reactor, the worm reduction gearbox plays a crucial, often overlooked, role in a multitude of chemical plant applications.
Considering the mechanism the Worm Reduction Gearbox
A worm reduction gearbox consists of a worm, a screw-like gear, meshed with a worm wheel, which resembles a spur gear. When the worm rotates, it drives the worm wheel, resulting in an important reduction in speed and a corresponding increase in torque. This speed reduction and torque multiplication are the fundamental benefits that make worm gearboxes so valuable. Gamma Gears is worm reduction gearbox manufacturer in Ahmedabad, Gujarat, India.
Key Applications of Worm Reduction Gearbox in Industrial Chemical Plants Equipment:
The unique advantages of worm reduction gearboxes make them indispensable in a wide range of chemical plant applications:
Agitation and Mixing: Chemical reactions often require precise and consistent mixing. Worm reduction gearboxes are used to drive agitators and mixers in reactors, ensuring thorough blending of chemicals and facilitating efficient reactions. Their high torque output is crucial for handling viscous fluids and maintaining reliable mixing speeds.
Conveyor Systems: Chemical plants rely heavily on conveyor systems for transporting raw materials, intermediate products, and finished goods. Worm reduction gearboxes power these conveyors, providing reliable and controlled movement of materials throughout the plant. The self-locking feature is predominantly useful in tending conveyors to prevent rollback.
Pumping Systems: Many pumping systems in chemical plants require an exact flow rate and pressure. Worm reduction gearboxes manufactured by Gamma Gears are used to drive pumps, providing the necessary speed reduction and torque amplification to deliver the preferred performance. This is essential for accurate dosing and transferring fluids to various process stages.
Valve Actuation: Monitoring the flow of liquids and gases is crucial in chemical plants. Worm gearboxes are used to actuate valves, providing precise and reliable control over flow rates and pressures. The self-locking feature ensures that valves remain in the desired position, even in the event of power outages.
Extruders and Pelletizers: In polymer production, worm gearboxes are used to drive extruders and pelletizers, shaping and sizing the final product. Their high torque capability is essential for processing viscous polymers and achieving the desired product characteristics.
Hoisting and Lifting Equipment: Maintenance and repair operations often require the use of hoisting and lifting equipment. Worm reduction gearboxes from Gamma Gears provide the necessary power and control for these tasks, confirming safe and efficient lifting of heavy components.
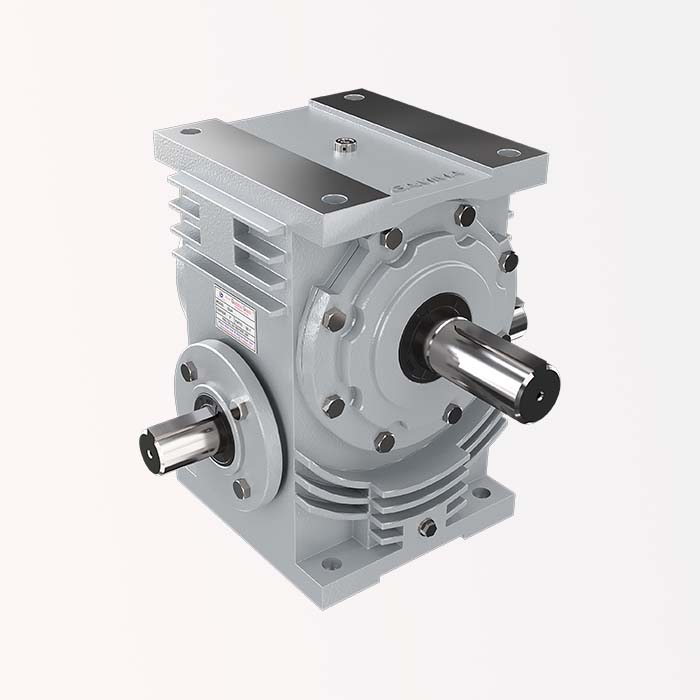
Concerns for Worm Reduction Gearbox Maintenance
Selecting the right worm reduction gearbox for a specific application requires careful consideration of factors such as the required input and output speeds, torque requirements, operating environment, and duty cycle.
Proper lubrication, regular inspection, and timely maintenance are also vital for ensuring the long-term reliability and performance of worm gearboxes. Gamma Gears is one of the world best worm reduction gearbox manufacturing company in Ahmedabad, Gujarat, India.
Worm reduction gearboxes are essential components in industrial chemical plants equipment, serving as critical links between power sources and process machinery. Their primary function is to transmit mechanical power from electric motors to equipment like mixers, pumps, centrifuges, agitators, and conveyors, adjusting speed and torque as needed for optimal performance.
In industrial chemical plants equipment, where processes often run continuously under harsh and corrosive conditions, so that contact to Gamma Gears as our gearboxes are designed for durability, reliability, and high efficiency.
At Gamma Gears, the materials used in gearboxes for industrial chemical plants equipment are carefully selected to withstand corrosive chemicals, high humidity, and extreme temperatures. Stainless steel, coated metals, and specially treated alloys are commonly used to make sure long-term resistance to wear and corrosion. Sealing systems and proper lubrication are also critical to protect internal components and maintain performance.